Understanding Porosity in Welding: Discovering Causes, Impacts, and Prevention Techniques
As specialists in the welding sector are well aware, understanding the causes, effects, and avoidance strategies connected to porosity is vital for attaining durable and dependable welds. By delving into the root causes of porosity, examining its destructive impacts on weld top quality, and exploring efficient avoidance methods, welders can boost their understanding and skills to create top notch welds consistently.
Usual Root Causes Of Porosity
Contamination, in the kind of dirt, grease, or corrosion on the welding surface, develops gas pockets when heated, leading to porosity in the weld. Inappropriate protecting takes place when the shielding gas, frequently used in processes like MIG and TIG welding, is unable to totally protect the liquified weld swimming pool from reacting with the surrounding air, resulting in gas entrapment and succeeding porosity. Furthermore, insufficient gas coverage, typically due to wrong flow rates or nozzle positioning, can leave components of the weld unsafe, enabling porosity to develop.
Results on Weld Quality
The visibility of porosity in a weld can dramatically endanger the total high quality and honesty of the bonded joint. Porosity within a weld produces spaces or cavities that compromise the framework, making it much more susceptible to fracturing, deterioration, and mechanical failing.
Additionally, porosity can prevent the effectiveness of non-destructive testing (NDT) techniques, making it testing to spot other defects or gaps within the weld. This can lead to substantial safety and security concerns, especially in critical applications where the structural honesty of the welded components is vital.
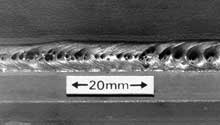
Avoidance Techniques Introduction
Given the destructive influence of porosity on weld quality, reliable prevention strategies are vital to maintaining the structural honesty of bonded joints. Furthermore, choosing the suitable welding criteria, such as voltage, existing, and take a trip rate, can assist reduce the risk of porosity development. By including these avoidance methods right into welding practices, the occurrence of porosity can be substantially lowered, leading to more powerful and more reliable welded joints.
Significance of Appropriate Shielding
Proper securing in welding plays a vital function in preventing climatic contamination and making certain the honesty of welded joints. Shielding gases, such as argon, helium, or a mix of both, are generally made use of to secure the weld pool from reacting with components in the air like oxygen and nitrogen. When these reactive aspects come into call with the hot weld swimming pool, they can trigger porosity, leading to weak welds with minimized mechanical buildings.
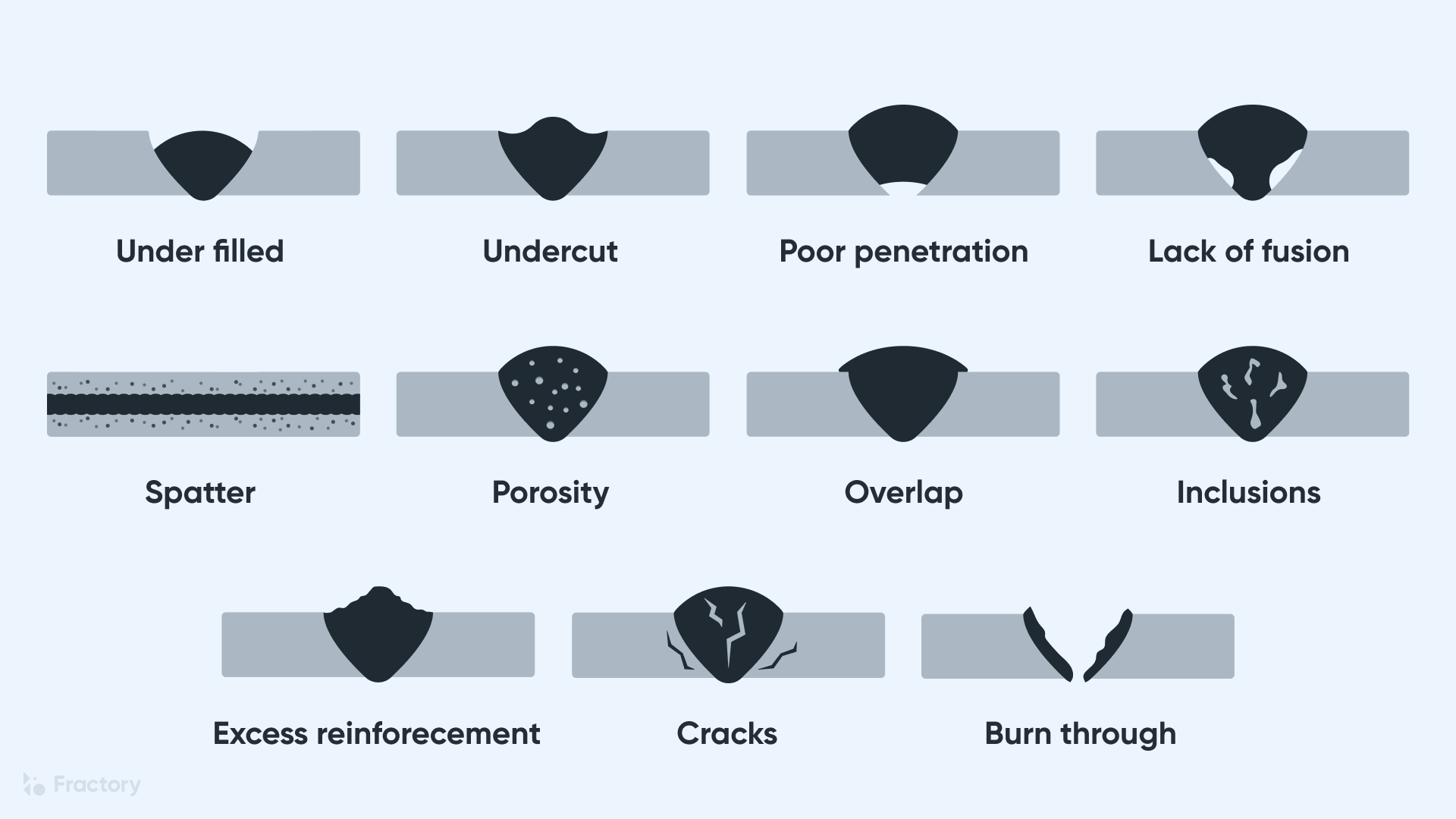
Inadequate protecting can lead to numerous flaws like porosity, spatter, and oxidation, compromising the architectural honesty of the welded joint. Consequently, adhering to proper protecting techniques is vital to generate top quality welds with minimal flaws and make sure the long life and reliability of the welded parts (What is Porosity).
Tracking and Control Techniques
Just how can welders properly monitor and regulate the welding procedure to guarantee optimum results and stop flaws like porosity? By constantly keeping an eye on these variables, welders can determine discrepancies from the perfect conditions and make instant adjustments to protect check my reference against porosity look at more info development.

Furthermore, executing proper training programs for welders is important for keeping track of and controlling the welding procedure successfully. What is Porosity. Educating welders on the importance of maintaining consistent criteria, such as appropriate gas shielding and travel rate, can assist protect against porosity problems. Regular analyses and accreditations can additionally make sure that welders excel in monitoring and controlling welding processes
In addition, making use of automated welding systems can enhance surveillance and control capabilities. These systems can precisely control welding specifications, lowering the probability of human mistake and ensuring constant weld quality. find out here By integrating innovative monitoring modern technologies, training programs, and automated systems, welders can successfully keep an eye on and regulate the welding process to decrease porosity defects and accomplish high-quality welds.
Verdict
